Emission of material from a source called target and depositing it on a substrate kept in a vacuum chamber is called as sputtering. Required deposition pressure is maintained inside the chamber during the sputtering process. Materials with high melting points are easily sputtered and their thin films are prepared by using sputter deposition technique while it is impossible with other tecniques to evaporate these materials.
Also the composition of the sputtered thin films is similar to that of the source material and also the adhesion of the thin films of the material over the substrate is better than that in the evaporated thin films. Other advantages in this method of deposition are the usage of sputtering source without any hot parts and the compatibility of the whole set-up with reactive gas such as oxygen. The sputtering gas is normally an inert gas such as argon. Initially negative charge is applied to the target which causes plasma or glow charge and sputtering starts. The high speed positive charged gas ions, ie the ionized A+ ions generated in the plasma region are attracted towards the negatively biased target material and collide with it making a momentum transfer. These collisions eject atomic size particles from the target and allow them to deposit as a thin film on the surface of the substrate which is connected with the positive electrode. When the ionized A+ ions hit the surface of the target material, secondary electrons are also produced which help further ionization process in the chamber. When the sputtering gas pressure is increased, the ionization probability increases and hence the number of ions and the conductivity of the gas also increase which reduces the breakthrough voltage. This generates stable plasma and thus sufficient amount of ions are available during the deposition period for sputtering the target material.
Thin Film Deposition is the technology of applying a very thin film of material – between a few nanometers to about 100 micrometers, or the thickness of a few atoms – onto a “substrate” surface to be coated, or onto a previously deposited coating to form layers. Thin Film Deposition manufacturing processes are at the heart of today’s semiconductor industry, solar panels, CDs, disk drives, and optical devices industries.
PVD processes are vacuum processes, which do not involve the use of hazardous chemical agents (PVD)
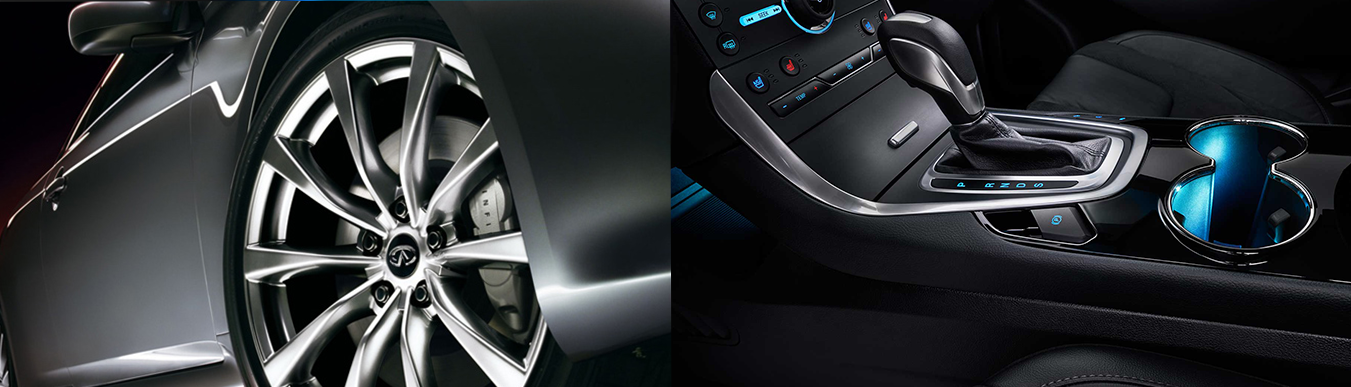